Combiner Box Inspection Checklist
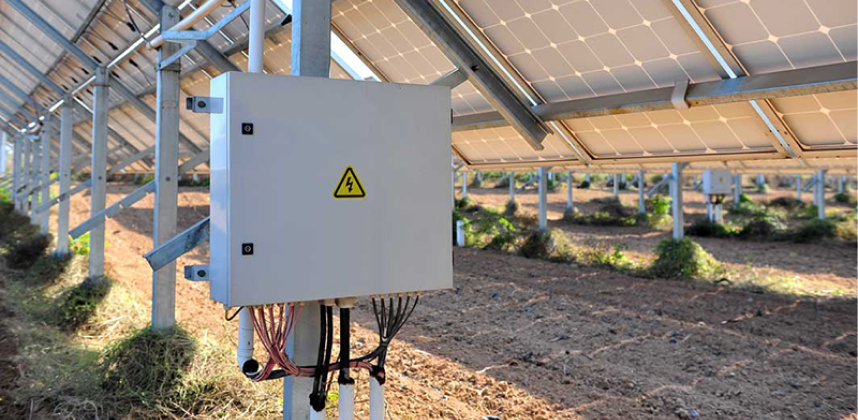
We do a lot of solar PV and renewable energy asset inspections here at HelioVolta and SolarGrade! Every time we visit a site, we use the SolarGrade platform to guide our workflow and document our findings.
Here are 17 things we look for every time we approach a combiner box:
1. Missing/Improper Label
Improper labeling can be a risk to personnel and should conform to applicable code, AHJ requirements and site drawings.
2. Pest Ingress
Pest intrusion may result in unintended current paths or component damage and can result in an electric fault.
3. Damaged Enclosure
Damage to the enclosure may result in a mechanical impact on contained components and can also compromise the protection rating of the enclosure.
4. Damaged Handle
This damage may result in limited component operation and may pose a system reliability risk.
5. Water Ingress
This may result in component protection failure. Without proper component protection electrical failures and thermal events may occur.
6. Corrosion
Corrosion will degrade the long term durability of the component and may compromise the enclosure rating.
7. Weep Holes
Weep holes help drain moisture in the enclosure, reducing corrosion and electrical failure risk.
8. Debris
Debris may result in unintended circuit paths or leakage current and can result in an electric fault.
9. Missing Duct Seal
Duct seal is used for wire management in enclosures and helps avoid dust, moisture and pest ingress.
10. Gasket Missing/Loose
Improperly installed or missing gaskets may result in moisture ingress.
11. Missing Torque Marks
Torque marks are necessary to assess if fasteners/connections have been properly torqued. Under-torqued fasteners may come to loose which may result in mechanical damage or bad connections. Over-torqued fasteners may result in improperly seated hardware.
12. Improper Wire Terminations
Improper termination may result in electric arcing, higher resistance connection, overcurrent instances and overheating.
13. Grounding
Non-current carrying conductors must be grounded for site safety and component protection.
14. Sharp Edges
Over time, with thermal expansion and contraction, wire insulation may abrade against sharp edges and result in an electrical short which may lead to a fault or thermal event.
15. Wire Management
Improper support, routing and protection of wires can lead to UV degradation, exposure to sharp edges, insulation damage, contact with moving parts, and improper wire bend radius.
16. Improper Enclosure Installation
With improper installation (refer to manufacturer specs), component protection may not be satisfied. For example, installing horizontally rather that vertically (if specified), leading to insufficient enclosure moisture egress.
17. Hotspot
Hotspots indicate a higher resistance connection which may result in component breakdown and electrical failure. We use a thermal camera to find hotspots.
We use SolarGrade to make sure we’re consistent and efficient, each time we go out into the field👨🏻🔧📲📝. See how it works for yourself at SolarGrade.io!