Connector Findings from Hundreds of Inspections
July 19, 2021
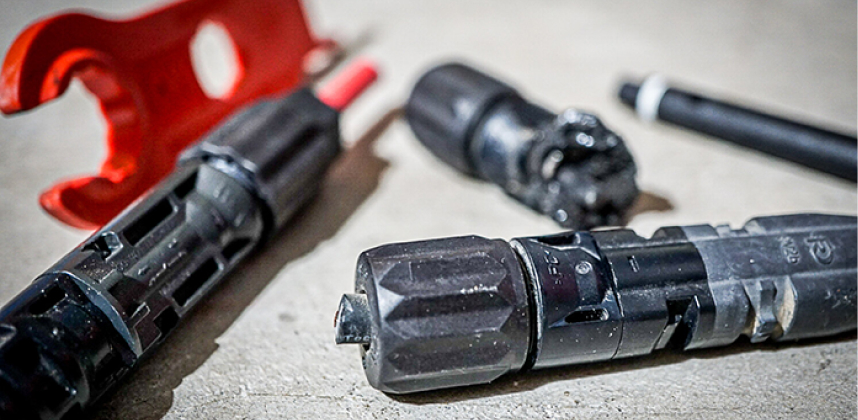
Cross-Mating & Compatibility
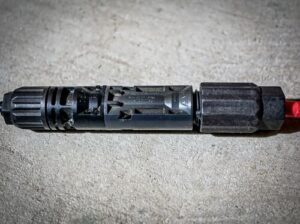
This is a huge problem in the industry. Since the MC4 type connection became the standard, lots of competitors created an “MC4 compatible” connector. For some years, the rules of compatibility were not fully clear or understood by the masses, and even today, not everyone is clear about it.
Connectors get tested as part of their certification process (EN50521 & UL6703) to ensure safety. However, different brands of connectors, one MC4 type female of brand X and one Male of brand Y don’t typically go through this process. This means that the term “compatible” is only on the shape of the termination and nothing else. It is for this reason that connectors must never be cross-mated unless they have been tested and certified together as a single component (this rarely happens for obvious reasons).
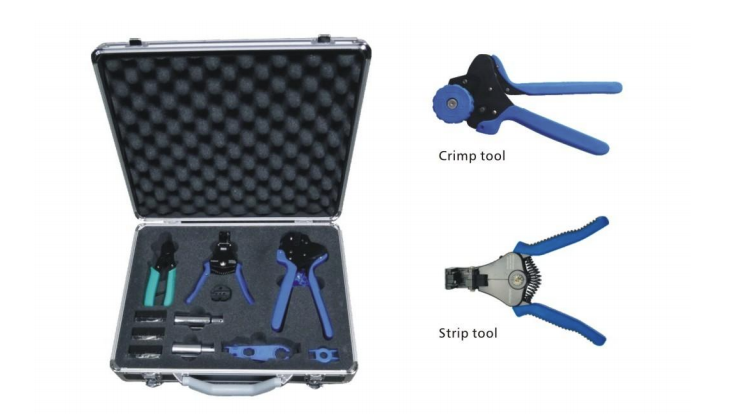
Additionally, few people realize that the tools used in the certification process are also part of the certification. This means that technically, you can only use the crimping tools provided by the manufacturer to make connectors in the field.
Factory-Made & Field-Made Home Runs
Related to the above point, even when trying to do things right, you or your team can run into this problem:
Let’s say you bought solar modules from XYZ, and they come with Amphenol (MC4 “compatible”) connectors from the factory but your local distributor only has Stäubli MC4 connectors for your field-made home runs. If you decide to do things right, you run into a warranty dilemma with the module manufacturer. Why? Because to use the same connector as the home runs, you will have to cut both ends of the strings and replace the factory-made connector with a field-made connector of the same typ e.
The best solution is to request that the module manufacturer provide additional connectors for the home runs. (Also ask for the certified crimping tools too!)
Additionally, module manufacturers will typically certify their modules with several connectors to have flexibility depending on supply-demand constraints. And guess what? In most cases, manufacturers don’t specify the connector type in their specification sheets. Module manufacturers sometimes don’t even 100% know which connector they will use until they start manufacturing. Do you see now why this is an issue?
Field-Made Connectors
This is also a pretty serious problem we encounter over and over.
- Not following the proper crimping procedures and torque specifications in the field. These specifications are detailed and vary from manufacturer to manufacturer.
- Not using the right tools (only the certified and approved by the connector manufacturer are the ones that should be used). This is always an issue, there are many non-certified tool options in the market.
- Lack of training. Making connectors in the field is not trivial, it requires training and practice. Quality control should always be required.
It all comes down to procedures, tools, and training. There is a great shortage of qualified solar professionals with experience and training, mostly due to the industry’s rapid growth: demand is exceeding supply.
Counterfeits
There are tons of counterfeit connectors out there claiming to be Stäubli, Amphenol, etc. Always review a few connectors closely and look for the seals and distinctive marks from the original manufacturers.
Even after all these years and we still get tricked sometimes. Here’s a photo from Wikipedia about MC4 solar connectors that shows counterfeit parts:
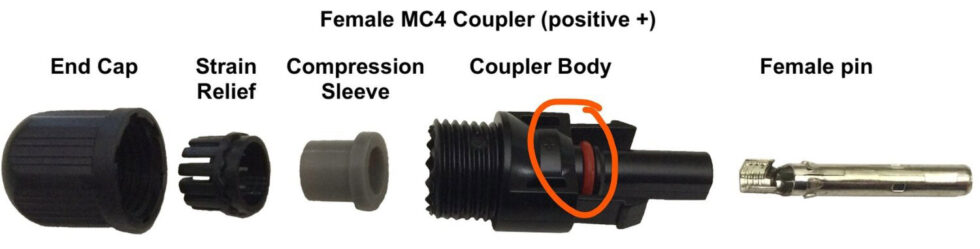
In this case, Stäubli does not use red O rings in their connectors, which tells us this is a counterfeit.
Below is another example that talks about the same O-ring issue in New Zealand.
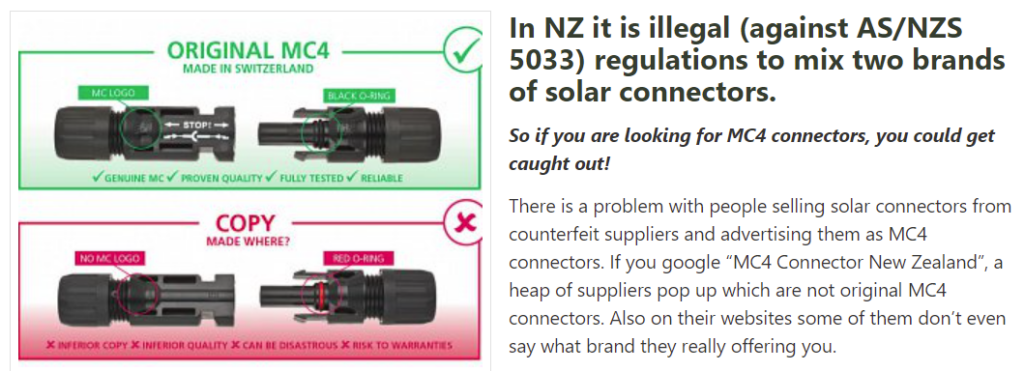
Just be mindful, fake connectors are out there, and some of them might have a questionable ability to last 25 years in the field.
Un-capped Connectors, The “Silent killer”
Another serious problem that no one talks about. When installing or replacing modules, sometimes, the leads and connectors will remain hanging for more than a few days, in some cases longer, and sometimes, during this time, the site might suffer rain events, wind, storms, etc.
Then, life goes on, and there’s a calm after the storm, crews go back to continue with the installation and stringing processes. Moisture or particles (contamination)get trapped when closing connectors. Let time do its thing and these connectors will corrode faster, being more prone to increased resistance, leading to overheating, and then this thermal cycle repeats until they fail.
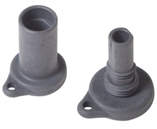
So, the solution to this is to string modules as soon as they get installed, limiting the exposure to the elements. And if they must be left sitting un-stringed, use caps to prevent moisture and other particles from entering inside the connector.
Serial defects
These are not common but there have been notorious cases of serial defects with connectors. These cases tend not to be publicized for obvious reasons.
- In 2017, SolarWorld recalled 97,000 Amphenol UTX connectors used in their modules produced from November 2016 through December 2016. The connectors could develop microscopic cracks that allow moisture to leak into them while the system is producing electricity, posing an electrical shock hazard.
- In 2018, according to Business Insider, Tesla started an initiative called Project Titan to replace hundreds of thousands of Amphenol Helios H4 connectors.
The Difficulty of Locating Connectors On-Site
This is more of a best procedure or practice than an issue. Connectors are everywhere on-site and usually underneath the modules and racking. They are difficult to find and difficult to locate.
In multiple instances, we’ve come across faulty connectors that we could not address right away and had to manually describe or annotate the exact location, which can make follow-up work difficult.
This is one of the reasons we added geolocation capabilities in SolarGrade, our solar and energy storage inspection software, to be able to allow technicians to be more efficient and effective in performing corrective action and their day-to-day work.
References:
- AMPHENOL HELIOS H4 ASSEMBLY INSTRUCTIONS
- https://ecsnz.com/blog/2016-03-07-the-most-used-and-tested-pv-connector-worldwide
- https://en.wikipedia.org/wiki/MC4_connector
- https://www.solargrade.io