Key Lessons About Solar Connectors
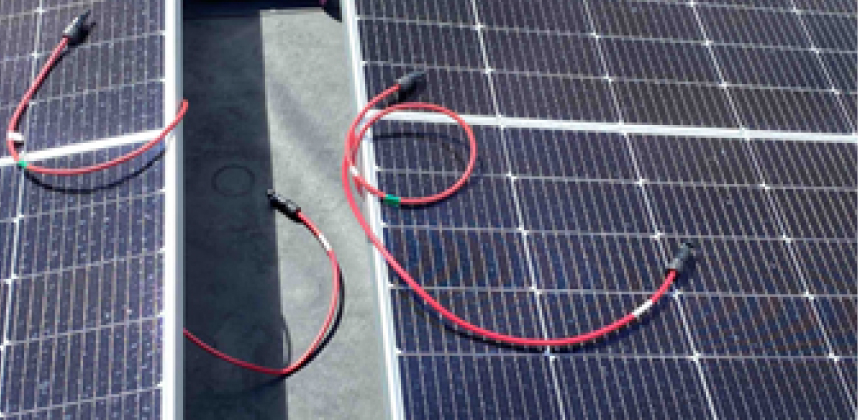
Why solar connectors?
Because connectors usually don’t get the attention they deserve. They are a key component of a solar system and hold an important function: to provide a low-resistance connection between solar modules and other components while maintaining their integrity under extreme weather conditions for more than 25 years.
Crazy, right? A piece of “plastic” that is exposed to the elements for more than 25 years, think about it.
Solar connectors are on the top of the list of root cause components that tend to cause the most severe impact when issues arise in solar systems: fires. According to a study by TÜV Rheinland, connectors, and connector-related issues, represent the single greatest risk to a PV system’s performance and safety.
So let’s understand a little better what connectors are, the types, the most common issues, and how to inspect them in the field.
What is a Solar Connector?
A solar connector is a type of DC electromechanical device used to join electrical conductors and create an electrical circuit. They typically have two removable parts, the Male or Plug, and the Female or Socket.
A curiosity: I have seen a lot of people confusing which part is the Male and the Female. The reason is that the plastic body is shaped backward, however, the metal pin is what drives the gender nomenclature. So, keep this in mind.

Understanding modern connectors requires looking back in time.
The National Electric Code, NEC, requires that any connection above 50V must be made by a licensed electrician. This was an issue, so a few companies around 2000 came up with solutions to address this requirement. They created a push-fit connector that met the definition of a convenience receptacle, meaning they could be (legally) connected together by anyone. Two players became the most common connectors during this period, the Radox connector and MC3 connector by Multi-Contact, both looked like weather-sealed phono jacks.
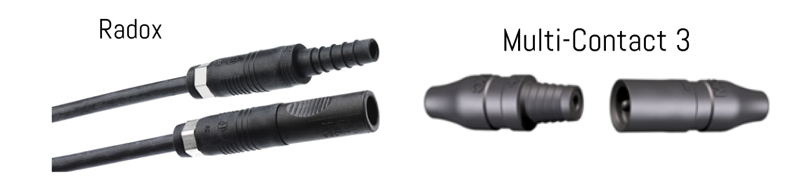
In 2008, the NEC came up with a new requirement to prevent people from opening connectors under load. Now, connectors must have “positive locking” meaning that could be plugged by hand, but could only be unplugged by a special tool.
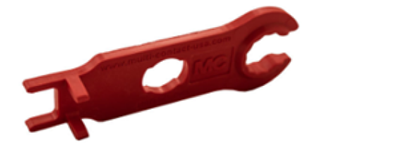
Myth: The un-locking tool can be used to torque the end cap of connectors. When it slips means that it is at the right torque. This is COMPLETELY FALSE. These tools are designed to help during connector assembly to get the first torque, however, a certified tool (yes, because the tool used to made the connector also needs to be certified as part of the assembly) should be used to properly torque connectors.
Continuing with the story, Radox, one of the main players at that time, did not come up with a new connector version to address the new requirement and the rest is history. Multi-Contact USA and Tyco Electronics, also a US company, came up with a new connector that complied with the new requirements.
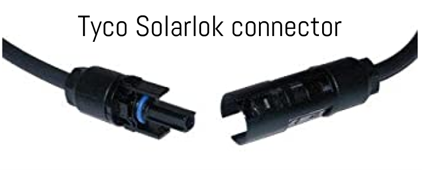
Tyco’s connector was more annoying to disconnect in the field and Multi-Contact slowly gained more popularity to become the market leader.
MC4 ultimately became the “industry standard” or “most common” solar connector. The MC4 stands for Multi-Contact (now Stäubli Electrical Connectors) and the 4 for the 4 mm diameter contact pin.
Below an exploded view of Stäubli MC4 connector:
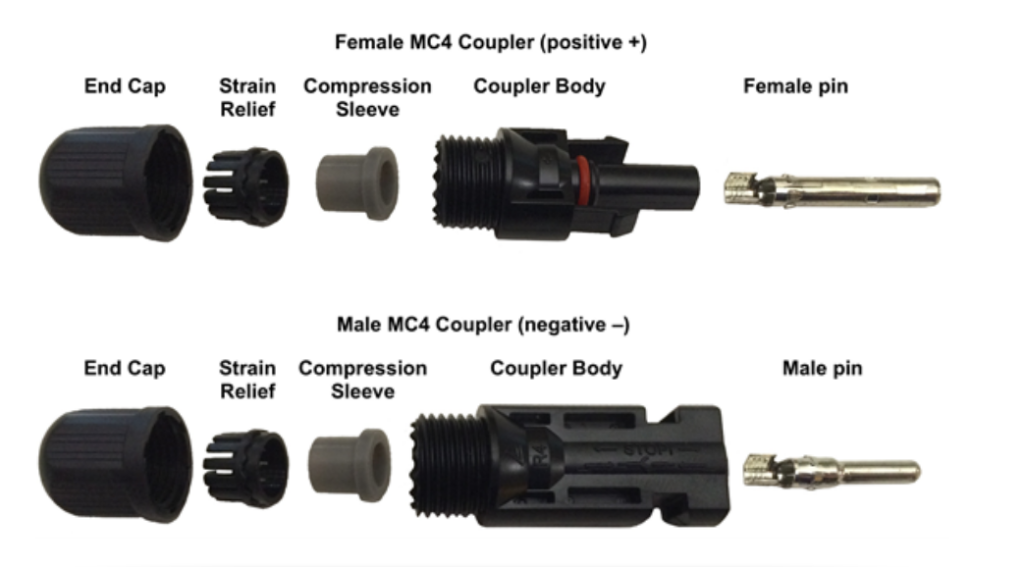
In 2008, Amphenol came up with a connector that has the same MC4 shape (the industry at the time called it “MC4 Compatible”) the Helios H4. Since 2008, there is a long list of MC4 connectors.
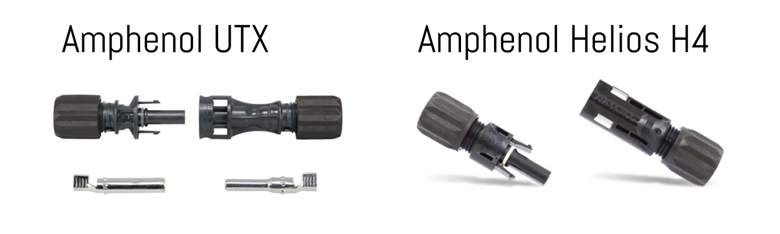
One of the latest code updates about this topic is Section 690.33(C) of the NEC 2020 that says, “Where mating connectors are not of the identical type and brand, they shall be listed and identified for intermatability, as described in the manufacturer’s instructions.” And the term intermatability is used in UL 6703, “Connectors for Use in Photovoltaic Systems”. This reinforces the fact of non-compatibility unless it has been tested together.
The image below shows a few other connector samples to be aware of.
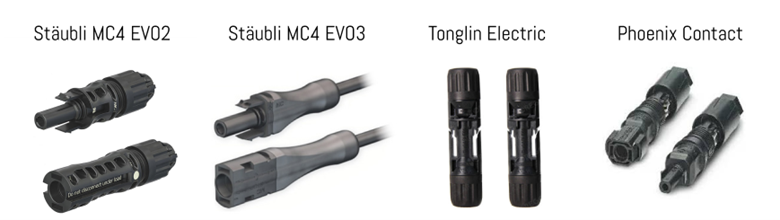
Key Features of Solar Connectors
- Interlockable
- Water and dust resistant, typically IP67 or 68 (max IP)
- UV resistant
- Double-insulated
- Able to handle up to 1500Vdc
- Able to handle up to 30A
- Temperature range -40°C to +90°C
Here a list of the most common issues we have come across in our professional career:
- Cross-mating and connectors compatibility.
- Factory-made – field made compatibility.
- Field-made connectors.
- Counterfeits
Interested in learning more about the connector issues our team has observed in the field? Head to another article on our blog: “What We Learned About Connectors from Hundreds of Solar Inspections“.
References and Credits
- All photos are from the manufacturers’ websites, so thanks to Tyco Electronics, Amphenol, Staubli, Radox, Tonglin Electric, Phoenix Contact
- https://en.wikipedia.org/wiki/MC4_connector